The process to make M.S. Billet is mentioned below.
We first need to collect Scrap, sponge iron and some casting. The M.S. scrap is charged in the induction Melting furnace with the help of cranes and the power is supplied to it. When the current passes through the copper coil of the induction furnace, the Electromagnetic force is generated. The induced Current in the scrap generates heat and adds the heat for melting of scrap. The metallic scrap is than melted when the temperature reaches to its melting point.
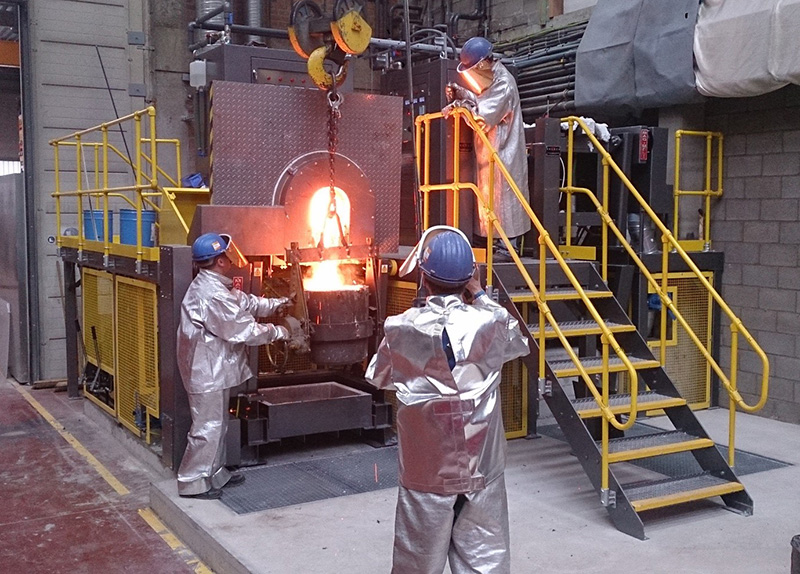
Process of Melting
The steel scrap is charged in ihe Induction Melting Furnace and power is switched on. When the current passes through the copper coll of tFre lnduction Furnace, Electromagnetic force is generated The induced Eddy Cutrent in the scrap generates heat and adds the heat for melting of scrap. The metallic scrap gets melted when the temperature reaches to its melting point.
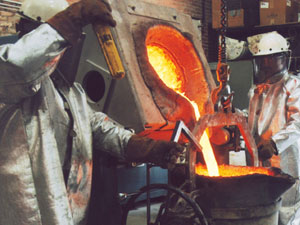
Process of De-Slagging
De-slagging operation is done as and when required by tilting the furnace when the slag volume is high enough to interfere with the scrap charging. Normally slag-off is done for twice or thrice in a batch depending on the charge mix and its quantity. When the furnace is filled with around 60% liquid rnetal, sample is taken to check the chemistry of the rnetal, before further charging of the scrap. At the end of the heat, requisite quantities of Ferro alloys are added to the liquid metal to acquire desired chemical composition.

Process of Pouring Metal
After attaining the intermediate or final composition depending on the further process, liquid metal from Induction Furnace is poured into a cured ladle at around 1620-1650C. Nitrogen is then purged to ladle through bottom porus plug for hornogenization of temperature and chernistry. After this, the ladle is transferred to the Continuous Casting Machine (CCM) for casting Billets. The ladle is placed on the tundish of Continuous Casting Machine (CCM). A tundish is a broad, open container or a resetvoir in the top part of a machine into which molten metal is poured having one or more holes in the bottom. The tundish allows a reservoir of metal to feed the molten metal to Continuous Casting Machine (CCM). Figure 'i' shows general arrangement of Continuous Casting Machine (CCM) used for production of MS Billets.
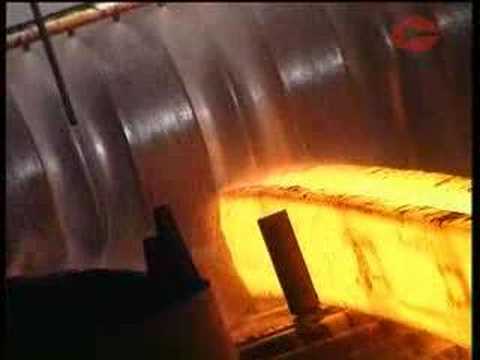
Process of Finishing
A flexible dummy bar storage unit is stored above the discharge roller table. This dummy bar system is used to set the Caster for Casting. The dummy bar inserted in the reverse way up till the mouth of the cable where it is fused with the molten metal in the tundish. Once the casting is started, the cast rolls formed the dummy bars towards the exit drawing metal attached to it continuously. The withdrawal of the billets is done by using flame cutters. The magnets then arrange the billets in groups. The billets are all set to cool and prepared for making and dispatch.